В статье рассказывается:
- Что такое система бережливого производства
- Кто стоял у истоков бережливого производства
- Философия бережливого производства: концепция и основные принципы
- Цели бережливого производства
- Преимущества и недостатки бережливого производства
- Этапы организации бережливого производства
- Потери в бережливом производстве
- Основные инструменты бережливого производства
- Бережливое производство и персонал
- Правила и условия успешного внедрения бережливого производства
- Примеры внедрения бережливого производства
- Сферы применения бережливого производства – готовые решения для всех направлений
- Бережливый бизнес в сфере продажи товаров и услуг
- Где брать информацию по бережливому производству: список лучших книг про бережливое производство
-
Чек-лист: Как добиваться своих целей в переговорах с клиентамиСкачать бесплатно
Сотни предприятий и компаний в России мечтают взять на вооружение бережливое производство, вот только не все до конца понимают, что это за система и как ее правильно внедрить. Некоторые считают ее волшебной палочкой, которая в одночасье решит все проблемы фирмы. На самом деле методология предусматривает кропотливый труд над всеми бизнес-процессами компании, чтобы выявить реальные потери и исключить их.
Бережливое производство – это не пошаговый план того, как из пункта А попасть в пункт Б. Это набор инструментов, каждый из которых подразумевает тот или иной набор действий для минимизации потерь. Причем для промышленности будут полезны одни методы, для торговли – другие, а для стартапа – третьи, для иных фирм – решения, вобравшие в себя черты разных вариантов. Со стороны все звучит очень сложно, но, если разберетесь в основах бережливого производства, у вас сразу все встанет на свои места.
Что такое система бережливого производства
Под бережливым производством понимают методы ведения хозяйственной деятельности, направленные на оптимизацию всех процессов, уменьшение затрат и объёмов отходов, поддержку инноваций и сокращение времени создания конечного продукта.
Эта система, иначе называемая Lean manufacturing, позволяет буквально каждому сотруднику видеть и выявлять потери, действовать так, чтобы ценность выпускаемого продукта неизменно росла.
По сути, если коротко отвечать на вопрос о том, что такое бережливое производство, можно сказать, что это максимально возможное сокращение расходов и одновременное повышение потребительской ценности.
Кто стоял у истоков бережливого производства
Первым, кто поставил производство и сборку автомобилей на поток, стал в своё время Генри Форд. На его заводах время выпуска одной машины стало исчисляться буквально в минутах, а не в часах и днях. Конечно, при массовом, серийном создании продукции используются идентичные и взаимозаменяемые компоненты, методы организации деятельности, что исключено в случае с ручной либо ремесленной работой.
Подобный подход поднял производственные показатели буквально до небес. С 1908 по 1927 годы Ford Motor Company выпустила свыше 15 миллионов авто.
В Японии в 1926 году Сакичи Тойода открыл завод Toyoda, делающий автоматические ткацкие станки. А через несколько лет тут стали выпускать автомобили и переименовали компанию в Toyota.
Позднее Эйдзи Тойода (племянник основателя завода) отправился в Дирборн, штат Мичиган, чтобы посетить расположенное тут самое крупное комплексное производственное предприятие Ford — Rouge Ford. Здесь за день выпускали около 8 000 авто. На Toyota в то время эта цифра достигала лишь 2 500 в год.
Эйдзи Тойода вник в производственные процессы и сделал вывод, что они неприменимы для Японии. Рынок здесь невелик, и притом весьма требователен. Заказчики ожидают индивидуального подхода, одним нужны роскошные авто, а других интересует компактность и доступность.
А Ford Motor Company была нацелена на массовое, объёмное производство. Особые пожелания потребителя тут никак не принимались в расчет. В итоге Toyota стала перед выбором: выпускать больше или всё же прислушиваться к покупателям, не гонясь за производительностью.
Совместно с Тайити Оно компании удалось выработать совершенно новый подход к процессу создания авто. В результате этого сотрудничества родились уникальные идеи, получившие название «Производственная система Toyota» или Toyota Production System. Система оказалась по-настоящему революционной и стала основой концепции бережливого производства физических товаров.
Философия бережливого производства: концепция и основные принципы
В основе бережливого производства как новой управленческой концепции лежит постоянное стремление к сокращению потерь как в цехах, так и в офисах. Данный подход часто называют «lean-производством» и «lean-технологией». Применительно к конкретному случаю — это «производство без излишеств», к чему, собственно, каждое предприятие и должно стремиться.
Принципы бережливого производства состоят в том, что компания в ходе создания продукта на каждом из этапов определяет его потребительскую ценность. Главная цель здесь – на протяжении всего процесса непрерывно устранять потери. Под ними подразумеваются операции или действия, которые никак не повышают ценность продукта, однако свои ресурсы компания при этом тратит.
Если говорить о видах потерь в бережливом производстве, то различают убыток одного рода и второго. К первым относят действия, в результате которых ничего не создается, но и обойтись без них невозможно. Это, к примеру, перевозка товаров или оформление документации для них. С точки зрения конечного потребителя данные операции не прибавляют продукту никакой ценности.
Потери второго рода тоже не приводят к созданию ценности, но их можно вообще убрать из производственного процесса и нужно даже обязательно постараться так сделать. Это, например, бракованные единицы продукции или слишком длительное ожидание.
Вообще все действия, которые выполняются в ходе работы предприятия, можно условно отнести либо к операциям, либо к процессам. При этом они делятся на:
-
прибавляющие ценность продукту;
-
не прибавляющие ценности продукту.
Философия бережливого производства в целом сводится к следующему:
-
Всегда можно найти способ оптимизировать любой процесс.
-
Главное – это ценность продукта.
-
Скорость и эффективность процессов нужно постоянно стараться повышать.
-
Первая задача оптимизации – уменьшение потерь.
К этому, собственно, и сводятся характерные особенности бережливого производства или Lean manufacturing.
Цели бережливого производства
Как свести потери к минимуму или устранить их совсем? Необходимо стремиться к целям, которые лежат в основе понятия бережливого производства:
-
Выпускать столько продукции, сколько её требуется на потребительском рынке.
-
Добиться полного отсутствия брака и притом производить товар или услугу идеального качества.
-
Быстро и безопасно доставлять до покупателей заказы.
-
С наибольшей отдачей задействовать материальные, трудовые и временные ресурсы за счет применения самых современных технологий.
-
Площади складов свести до допустимого минимума.
-
Добиваться того, чтобы буквально каждый сотрудник, используя собственный творческий потенциал, принимал участие в создании ценного продукта.
Преимущества и недостатки бережливого производства
Сначала о плюсах бережливого производства:
-
Экономия рабочего времени. Простой пример: есть работник, который, выполняя определенные действия на конвейере, вынужден постоянно использовать то один, то второй источник питания. На одно переключение уходит до 10 секунд, и это совершенно бесполезно потраченное, не добавляющее продукту ценности, время. А за смену таких переключений происходит очень много, то есть временны́е потери растут. Если действовать в соответствии с идеями бережливого производства, то нужно организовать один удобный источник питания (отвечающий правилам), чтобы не тратить ресурсы впустую.
-
Экономия площадей. Это достигается благодаря максимально продуманной организации пространства, когда тщательно подобран весь необходимый для работы инструментарий и удобные для него места хранения (чтобы всё было под рукой). В итоге удается лучше организовать управление производством, контролировать запасы, исключать вынужденные простои, а работники не тратят время на поиск деталей и орудий.
-
Контроль качества как готового продукта, так и буквально каждого этапа его создания. Характеристики от этого улучшаются, а брака становится меньше.
-
Экономное расходование денег за счет снижения расходов на всех этапах производства.
-
Стремление к совершенствованию. Буквально все сотрудники постоянно ищут пути улучшения собственных достижений и опережения конкурентов.
Минусы в концепции бережливого производства, как и в любой другой системе управления, тоже есть:
-
Сбои из-за проблем с поставками. Так как принцип бережливого производства предполагает сокращение складских площадей, то запасов остается лишь необходимый минимум. И если вдруг поставщики или транспортники подвели с поставками, для предприятия это может обернуться трагедией. Но эти контрагенты не всегда согласны продавать мелкими партиями по жестко установленному графику, им это может быть невыгодно (из-за накладных расходов). Как результат – сбои в производственном процессе. Но и часто менять поставщиков – плохо для самого предприятия.
-
Большие расходы на внедрение. Нередко для организации бережливого производства требуется демонтаж и переоборудование заводских цехов. Плюс нужны средства на переподготовку и обучение персонала. Часто эти расходы так высоки, что подобная реорганизация оказывается попросту не по карману малому и среднему бизнесу.
-
Неприятие персоналом концепции бережливого производства. Глобальные перестройки и перемены в деятельности у многих вызывают стресс и нежелание работать дальше. Людям тяжело покидать, так сказать, накатанную колею. Плюс начинается усиленный контроль качества (специально для этого даже назначается сотрудник). Кроме того, не так легко найти руководителя, у которого хватит терпения и опыта для убеждения сопротивляющегося персонала.
-
Недовольство со стороны клиентов. Когда качество производственного процесса попадает в зависимость от эффективности поставщиков, любой сбой в доставках приводит к неудовлетворенности клиентов. Им приходится слишком долго ждать своих заказов.
Этапы организации бережливого производства
Выделяют следующие этапы внедрения бережливого производства:
-
Определение потребительской ценности товара или услуги. То есть в первую очередь нужно выявить действия, приносящие полезность потребителю, и действия, в которых нуждается лишь сам производитель.
-
Выявление списка оптимального числа операций, необходимых для создания ценного продукта. Налаживание производственной цепочки от начала планирования и до поставки готового изделия, одновременное сведение возможных потерь к минимуму.
-
Организация непрерывной цепочки действий, направленных на выпуск ценного продукта, глобальный пересмотр всего процесса его создания. Работа сотрудников выстраивается по принципам lean-концепции. Лишние операции убирают, оставляя лишь те, что придают ценность выпускаемому продукту. Простои и ожидания сводятся к минимуму (тоже за счет тщательного упорядочения всех действий). Если не хватает производственных мощностей и технологий – их внедряют, и т. д. и т. п.
-
Продукт подвергается так называемому «вытягиванию» со стороны потребителя. Суть термина в том, что компания стремится выпустить именно нужный покупателям продукт и лишь в требуемом количестве.
-
Все процессы на предприятии непрерывно совершенствуются. Применение бережливого производства – это не разовая акция, а изменения, внесенные в работу навсегда, на постоянной основе. При этом к поиску улучшений и возможностей для сокращения потерь привлекаются абсолютно все сотрудники.
Потери в бережливом производстве
По сути, на любом производстве, буквально во всех отраслях лишь небольшой процент времени уходит на создание ценности. Всё прочее – потери, то есть то, что для клиента не имеет никакого значения. Именно в таком ракурсе и рассматриваются все действия, процессы, функции и материалы. Клиенту не важно, за сколько километров везут к нему молоко и сколько раз работникам пришлось переставлять бидоны с ним.
Все эти действия не добавляют конечному продукту полезности, а значит, для клиента они не ценны. Система бережливого производства подразумевает рассмотрение каждого процесса с точки зрения его полезности для создания ценности. То, что не создает ценности (а это и есть потери), необходимо свести к минимуму.
Основных видов потерь в концепции Lean manufacturing различают семь:
-
товар выпущен, а спроса на него ещё нет (перепроизводство);
-
простой из-за отсутствия деталей, материалов, полуфабрикатов или даже требуемой информации;
-
лишние этапы и расходы в транспортировке (когда, к примеру, склады, цеха и оборудование расположены неудобно);
-
неэффективные шаги в процессе обработки, ставшие результатом ошибок, допущенных при проектировании (деятельности или самого продукта);
-
неверно организованная производственная или иная схема и скопившиеся из-за этого залежи запасов;
-
много лишних и ненужных перемещений людей во время рабочего процесса;
-
выпуск бракованной и дефективной продукции.
Негласно упоминают еще восьмую группу потерь, которая связана с недостаточным вниманием к человеческому фактору.
Количество и объёмы издержек можно минимизировать, если избавиться от вызывающих их предпосылок. В системе бережливого производства для этого есть целый ряд инструментов.
Основные инструменты бережливого производства
Чтобы бороться с потерями, нужно уметь их видеть, определять. В бережливом производстве для этого существуют специальные методы и инструменты.
Система «Канбан»
Это организация производства и снабжения, основанная на реализации принципа «Точно в срок». Она представляет собой набор карточек или иных визуальных маркеров («канбан»), с помощью которых обозначается число комплектующих, узлов при производстве готовой или находящейся в стадии изготовления продукции.
На предприятии канбан может выполнять две задачи:
-
Для процесса производства – это так называемый канбан изготовления: по нему видно, что нужно приступать к созданию продукции (либо следующему его этапу).
-
Для сотрудников – это канбан отбора (или перемещения), на нем информация о том, что данное изделие (заготовку) нужно переместить.
Канбан будет максимально эффективен, если при его использовании придерживаться следующих шести правил:
-
Процесс-потребитель заказывает именно столько готового продукта, сколько обозначено на карточке канбан.
-
Процесс-поставщик тоже выпускает именно то и именно столько, сколько указано в системе.
-
Если на канбан нет карточек, значит не нужно ничего выпускать и перемещать.
-
К любым материалам и деталям крепится карточка с прохождением производственной системы.
-
Детали с браком или в другом количестве (не таком, которое заявлено) не передаются на следующий этап производства.
-
Для понимания объёма запасов или выявления проблем нужно постепенно уменьшать на канбан количество карточек.
Картирование производственных процессов
Это когда материальные и информационные потоки графически отображаются на схеме, действуя по которой удается донести до конечного потребителя товар или услугу. Благодаря картированию становится видно, какие операции или затраты имеют низкую производительность. И тогда можно предпринять шаги по их улучшению.
За время формирования ценностей принимается период, достаточный для преобразования изделия до вида, в котором люди готовы будут его покупать. Потоком создания называют набор всех действий, выполняемых в процессе производства продукта. Вообще, почти на каждом предприятии потери доходят до 80 % (эта цифра подтверждается практикой).
Система 5S
Ещё один инструмент бережливого производства, применяемый для максимально эффективного использования рабочего пространства. Это позволяет экономить время и улучшать управляемость каждой зоны и всей схемы.
В рамках системы выполняется:
-
Сортировка.
-
Рациональное обустройство рабочих мест.
-
Уборка пространства.
-
Приведение к стандартам.
-
Постоянное усовершенствование.
Благодаря системе 5S в документации уменьшается число ошибок, формируется комфортная обстановка для работы, растет производительность труда. Какие-то новые управленческие методики при этом внедрять не обязательно, что является неоспоримым плюсом.
Система «Кайдзен»
Если в двух словах – это теория постоянного совершенствования. То есть, когда компания непрерывно стремится улучшать технологии и системы управления, использовать эффективные нововведения. Философия кайдзен касается всех процессов в компании и привлекает к участию буквально каждого сотрудника.
Плюсы данного подхода:
-
Система применима как для мелкого бизнеса, так и для громадных корпораций.
-
Внешне никаких изменений часто не видно, потому что они выполняются с небольшим шагом. А это означает, что для наблюдающих за вами конкурентов всё это остается незаметным.
-
Большая часть реструктуризации происходит на местах, поэтому внедрение кайдзен не требует особых затрат.
-
В процесс вовлекается весь персонал, если, конечно, цель предстоящих изменений и улучшений грамотно донесена до каждого.
-
Повышается качество готового продукта, сервиса.
В чем состоит главная концепция системы «Кайдзен»? На предприятии провозглашается идея о том, что ничто не статично, равновесия нет, и всё непрерывно нужно пересматривать. Поэтому изменения, пусть даже самые небольшие, вводятся все время, благодаря чему и происходит постоянный прогресс.
Полная визуализация
Подразумевает размещение на виду абсолютно всего, что касается производственного процесса: инструментов, деталей, операций, данных о результатах работы. Благодаря этому все участники знают, что происходит в системе и в каком она находится состоянии.
Визуальный менеджмент внедряется поэтапно, и шаги здесь такие:
-
Идёт организация рабочих мест.
-
Данные о безопасности труда, правила использования оборудования и выполнения операций, стандарты качества – всё это представляется визуально.
-
Результаты процессов и оценка их эффективности тоже отображается.
-
На основании визуализированных данных принимаются дальнейшие решения.
из разных ниш с ростом
от 89% до 1732%
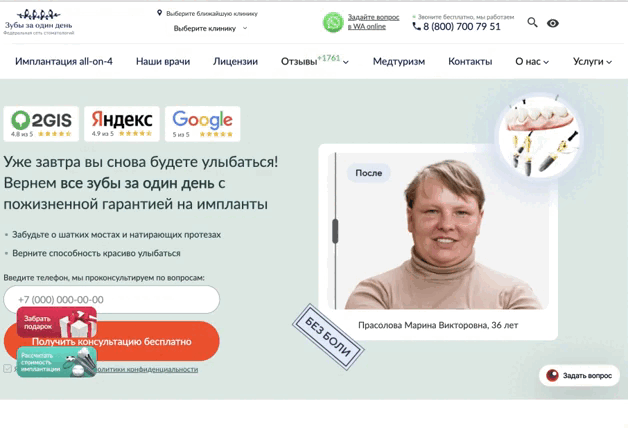
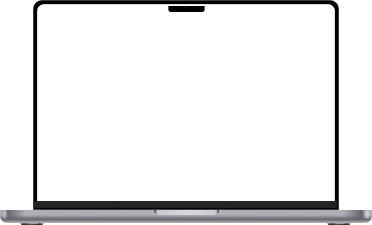
Принцип вытягивающего производства
Это когда от последующих операций к предыдущим идут сигналы о тех или иных производственных потребностях. Проще говоря, суть любой (даже малейшей) деятельности при использовании этого принципа сводится к тому, что:
-
Реализуются лишь заказы, поступившие именно от следующей операции.
-
Если для осуществления следующей операции производить ничего не нужно, значит, работа на время останавливается.
Подобный подход повышает экономическую эффективность проекта бережливого производства. Прибыль растет при увеличении скорости деятельность, а она растет при снижении объёмов запасов продукции. Их же становится меньше, если выпускается лишь то, что было необходимо и, соответственно, заказано.
Получается, каждый станок производит лишь необходимый для следующей операции продукт, именно благодаря этому происходит рост объёмов прибыли.
Бережливое производство и персонал
Чтобы технологии бережливого производство действительно успешно работали, необходимо проводить целенаправленное обучение персонала. Для этого существуют специальные программы, рассчитанные и на новичков, и вообще на сотрудников разных категорий. В учебный план входит изучение основных видов бережливого производства, используемого инструментария и критериев оценок результатов.
Персонал, обучающийся в свое свободное время, получает за это отдельную оплату.
По окончании занятий структура предприятия переформировывается. Из его подразделений образуются новые функциональные единицы с учетом требуемых потоков создания ценностей (товаров или услуг). В рамках концепции бережливого производства образуются рабочие группы (бригады), наделяемые ответственностью за внесение постоянных улучшений в процесс трудовой деятельности и со своими полномочиями, которые позволяют не согласовывать с вышестоящим руководством каждый шаг.
Источник: shutterstock.com
Бывает и такое, что младший персонал сопротивляется внедрению Lean. Это случается, когда принципы бережливого производства не донесены в полной мере до сотрудников. Нельзя начинать вводить подобные концепции просто по приказу, не объяснив как следует, что это и для чего делается.
Поэтому тут очень важно провести полномасштабное обучение персонала, вовлечь буквально каждого. Работники сами смогут находить эффективные решения для тех или иных ситуаций, когда изменятся их взгляды на все процессы трудовой деятельности. Тогда и экономическая эффективность проекта бережливого производства будет выше, а это, разумеется – в интересах компании.
Для реализации методологии бережливого производства нужно сначала подготовить условия:
-
Проведите обучение для персонала, правильно распределите человеческие ресурсы.
-
Сформируйте корпоративную культуру, направленную на продвижение новых методов работы и объяснение их ценности.
-
Сразу подайте идею бережливого производства так, чтобы все сотрудники были ею заинтересованы.
-
Меняйте мышление людей, учите правильно понимать потери и ценности.
-
Согласуйте работу всех отделов (маркетингового, финансового, IP, HR и др.), добейтесь взаимной поддержки.
-
Организуйте централизованное управление, обеспечьте финансовую поддержку внедряемой концепции.
После этого можно начинать пошагово организовывать в компании бережливое производство.
Примеры внедрения бережливого производства
Если говорить о российских предприятиях, то первопроходцами тут стали представители крупномасштабного промышленного производства. Это КамАЗ, «Группа ГАЗ», «ВСМПО-АВИСМА», «Русал», «ЕвразХолдинг», «Еврохим» и другие. Обычно, как ни печально это признавать, за консультациями обращаются предприятия, на которых появились серьезные проблемы. То есть снижается рентабельность, выходит больше брака, заказчики недовольны и т. д. и т. п. Компаниям приходится думать, как улучшить производство и снова войти в колею.
И тут хорошо вот что: когда они видят первый положительный эффект, то не бросают начатое, а продолжают действовать по нововведенным принципам, применение которых явно дает отличные результаты.
-
«Урал»
Внедрение Lean на автозаводе «Урал» (Миасс, член «Группы ГАЗ») началось в 2003 году. Это был кризисное время, когда продукции предприятия стало продаваться почти в два раза меньше. Благодаря применению методик бережливого производства удалось улучшить буквально все показатели. Об этом сообщил директор завода Виктор Корман в своем интервью журналу «Эксперт-Волга».
Ежегодная экономия средств сейчас доходит до суммы в 300–400 млн рублей, и внедрение Lean manufacturing продолжается с привлечением всё большего числа сотрудников. Таким образом выполняется одна из установок данной концепции о том, что в ней должны участвовать абсолютно все: и управленческий состав, и простые рабочие.
-
«КамАЗ»
Ещё один удачный пример организации бережливого производства. Здесь процесс начался в 2005 году, а еще раньше к преобразованиям приступили члены концерна «КамАЗ-Металлурия» и «КамАЗ-Дизель». И сегодня в разных подразделениях и компаниях группы работы в данном направлении не прекращаются.
Специально подготовленные менеджеры, защитившие по теме усовершенствования технологических циклов более 50 проектов, теперь сами обучают других сотрудников и подключают к процессу, причем не безрезультатно. К примеру, выяснилось, что в цехе пресс-форм ОАО «КамАЗ-Инструментспецмаш» девять станков вообще не задействуются. Их убрали и тем самым почти в три раза уменьшили показатель простоя оборудования.
Теперь ещё директор КамАЗа дал распоряжение оптимизировать расходы на содержание относящейся к предприятию земли, а это в целом 1 900 га. Незадействованные в производстве площади планируется освободить и продать либо сдать в аренду (чтобы получать от них прибыль).
-
ЭПО «Сигнал»
Пример из Саратовской области. Бывшее оборонное предприятие, делает приборы для аэрокосмической промышленности и аппаратуру, используемую в газовом хозяйстве. Главная проблема на подобных заводах – износ оборудования. Тут задача внедрения лин-технологий была передана на аутсорс. Специалистам хватило буквально нескольких дней, чтобы помочь сотрудникам выявить все технические неисправности и подготовить программу по их устранению.
Тут суть сводится к следующему: поддержание работоспособности оборудования – это задача не только ремонтников, но и операторов, работающих на конкретных станках и знающих на них каждую «трещинку».
Как оценить эффективность внедрения
Экономическая эффективность проекта бережливого производства оценивается по трем основным направлениям:
-
По показателям управленческой стратегии: удалось ли сформировать философию Lean production, насколько вовлечено руководство, каковы показатели KPI, доволен ли потребитель.
-
По персоналу: как идёт обучение, воспитание лидеров, чувствуется ли сплоченность в коллективе, сколько поступает качественных кайдзен-предложений, налажено ли в компании самообразование.
-
По процессам: насколько задействованы инструменты Lean, снижены ли потери, улучшается ли качество товаров (услуг) и сервиса, грамотно ли налажено взаимодействие с поставщиками, дилерами.
Эксперты-оценщики (каждый из них) по всем параметрам выставляют баллы, по которым потом выводится средний показатель.
Сферы применения бережливого производства – готовые решения для всех направлений
Сферы применения принципов бережливого производства очень разнообразны (хотя по названию кажется, что это подходит лишь для производственных предприятий). И тому есть масса подтверждений среди российских и зарубежных компаний.
Источник: shutterstock.com
Рассмотрим использование бережливого производства в различных сферах деятельности.
Концепция «Бережливый офис» и используемый при этом инструментарий
Всякие нестыковки случаются в любой компании:
-
Подошло время оплаты работы исполнителя, а договор не подготовлен.
-
Клиенту нужно уделить внимание, а менеджер не может найти нужные документы.
-
Срочно понадобилось дополнительное соглашение, а в принтере нет бумаги (вовремя не заказали).
Казалось бы, всё это мелкие нестыковки, однако они могут накапливаться и уже ощутимо мешать бизнесу. В подобных случаях офисные процессы явно требуют усовершенствования. Вот тут и пригодится методология «Бережливый офис», подразумевающая пересмотр и обновление его ресурсов, улучшение системы действий, устранение мусора.
Порядок действий при этом следующий:
-
Приведите в порядок рабочее место. Доступ к папкам, документам и канцелярским принадлежностям не должен быть ограничен. Помечайте материалы маркерами, цветными разделителями, наклейками. Зелёной обозначьте папку с договорами, синей – список сотрудников и т. п. Сделайте перечень с указаниями, что какой цвет значит, и сохраните эту информацию на Google-диске.
-
Сведите к минимуму запасы. Пусть на столе лежит лишь самое нужное. Не храните тут горы канцелярии (типа «потом пригодится»), ненужные файлы, неработающую технику.
-
Устраняйте потери. Сотрудники должны как можно меньше ходить по офису, перемещать документы.
-
Время ожидания тоже следует минимизировать. Пока менеджер ждет прихода клиента или звонка от него, он теряет время (а мог бы сделать что-то полезное).
-
Приучите себя к внимательности и сразу всё делайте правильно, чтобы потом не тратить время на выискивание и исправление банальных опечаток и т. п.
-
Сформируйте поток деятельности, точно распределите круг задач каждого сотрудника.
-
Не прекращайте совершенствоваться. Изучайте рабочие процессы и все время старайтесь их улучшать.
В качестве одного из инструментов бережливого офиса используется визуализация (lean-visualization). В сравнении с текстами, информация, представленная в виде схем и графиков, запоминается лучше.
Практически визуализацию можно задействовать так:
-
Подготовить наглядные инструкции по использованию оргтехники (новички смогут спокойно ею пользоваться сами и не просить о помощи коллег, тем самым мешая им работать). Такие подсказки можно сделать вообще для любого офисного оборудования (кофемашины, кондиционера и т. п.).
-
Создать список «быстрых» кнопок для звонка в тот или иной отдел (например, бухгалтерия – 1, ОТК- 2, производственный – 3, склад – 4 и т. д.).
-
Упорядочить документооборот. Отобразите на схеме, как должна двигаться документация по предприятию, чтобы не было путаницы, и чтобы это не отвлекало от других дел.
Помните, что многозадачность – это ещё не значит продуктивность. Хватаясь сразу за несколько дел, вы не можете нормально сосредоточиться ни на одном из них, что, разумеется, не лучшим образом отражается на качестве. И тут вам в помощь доска канбан. Поделите на ней задачи на три группы:
-
то, что еще требуется сделать;
-
то, что сейчас делается;
-
то, что уже сделано.
Текущих задач (в работе) должно быть не больше трёх, так проще сконцентрировать на них внимание.
Канбан сделайте в приложении (Jira, Trello, Asana, Bitrix24) или просто начертите на ватмане. Тогда весь рабочий процесс будет перед глазами, что упрощает контроль. Тут каждая задача записана, занимает своё место, и вам не нужно держать всё в голове и бояться что-то упустить.
Пробуйте применять разные инструменты бережливого офиса, подбирайте то, что лучше всего подходит именно вам, и вы увидите, как это отразится на результатах работы.
Концепция «Бережливый стартап»
Первым, кто сформулировал и стал применять понятие бережливого стартапа стал в 2011 году Эрик Рис, написавший об этом книгу «Бизнес с нуля». Главная суть Lean Startup — в итеративном подходе к выпуску продукта, который необходимо постоянно тестировать, получать обратную связь от покупателей и вносить соответствующие корректировки. При этом не нужно ничего детально планировать и вкладывать в проект серьезные средства.
Так становится ясно, что ценит клиент в продукте и задействовать лишь столько денег, сколько требуется для его выпуска. Причем бережливость затрагивает и потраченное время, и человеческие ресурсы (не только деньги).
Получается, что для стартапа не важны бизнес-планирование, четкая стратегия, личное обаяние владельца. Тут главное – выдать на рынок нужный, востребованный продукт. Lean Startup с помощью постоянного тестирования помогает довести до ума даже минимально жизнеспособный продукт (MVP). При этом задействуется Customer Development, Lean Canvas (пресловутые «Девять шагов построения бизнеса») и agile (ответ на клиентскую обратную связь).
Для стартапа первостепенно важно наличие востребованного товара (услуги). И концепция бережливого стартапа позволяет с минимальным риском преподнести потребителю именно такой продукт, которого он ждет (с оптимальным расходом денег, времени, кадров).
Главная цель – экономить ресурсы, пока не выработается модель, пригодная для масштабирования. В момент открытия бизнеса перспективы видны слабо, поэтому трудно определить достаточно точно, чего ждет потребитель. Lean Startup дает понять, что, во-первых, разработчики должны грамотно проанализировать обстановку и выявить, в чем именно нуждается целевая аудитория. А во-вторых, необходимо наладить возможность практического тестирования выдвигаемых гипотез, то есть получать эмпирические данные.
В ходе внедрения методики бережливого стартапа компания выявляет потребности своего будущего покупателя, подготавливает MVP, тестированием проверяет, отвечает ли он требованиям аудитории и нуждается ли последняя в таком продукте. Тут вот что ещё важно: lean – не волшебная палочка, которая продвинет вперед любой стартап. Просто если проект неудачный и бесперспективный, то данный подход поможет вам это разглядеть, осознать и не бросать на ветер деньги и иные ресурсы.
Основные принципы Lean Startup следующие:
-
Методика подходит для использования в любой сфере деятельности, если условия работы отличаются высокой степенью риска. Крупных компаний, подготавливающих для рынка новый продукт, это тоже касается.
-
Менеджмент задействуется именно такой, который подходит для рискованных условий.
-
Стартап должен непрерывно развиваться, изучать потребности своей целевой аудитории и обязательно проверять и подтверждать на практике правильность выдвигаемых гипотез.
-
Что особенно важно в Lean Startup, это как можно раньше узнать реакцию потребителя на MVP, выявить его недостатки и продолжить развитие, либо сделать пивот и двигаться совершенно в ином направлении.
-
Анализ инноваций, которые нужно тщательно изучать по всем показателям, чтобы понимать, насколько эффективен стартап.
Бережливый бизнес в сфере продажи товаров и услуг
В системе бережливого производства есть инструменты, позаимствованные из ритейла. Это: FIFO, размещение товаров в торговых залах, JIT, канбан, автономизация. Во многих книгах по этой теме за основу берется зарубежный опыт внедрения бережливого производства.
Но применение данной концепции к розничной торговле в России далеко не всегда проходит гладко, здесь это относительно новая, малознакомая методология. Рассмотрим подробно особенности этого процесса.
Признаки схожести экономических субъектов в розничной торговле
В данной сфере существуют свои особенности ведения дел. Но для начала не лишним будет выяснить, чем могут быть похожи организации, занимающиеся розничными продажами. Вот несколько характерных общих черт:
-
Производственные процессы автоматизированы или механизированы. Люди, работающие в таких компаниях, непременно используют машины, приборы, технические приспособления.
-
Система менеджмента. Если сотрудников больше 10, то необходима организация полноценного управления.
-
Создание ценности для клиента и постоянное её усовершенствование. На рынок необходимо выдать новый, уникальный продукт, либо непрерывно работать над улучшением того, что уже есть. Это главный процесс, вокруг которого выстраиваются стратегическое планирование и вся деятельность.
-
Способность конкурировать. На длительном промежутке времени это определяется тем, насколько компания способна удовлетворять запросы потребителя.
Разумеется, есть и другие схожие черты у подобных организаций, но даже по перечисленным ясно, чем характеризуется Lean retailing в розничной реализации.
Различия предприятий в отрасли
Компании в розничной торговле имеют свою определенную структуру, стратегию поведения на рынке и прочие особенности. Если говорить об основных отличиях ритейла, то их выделяют пять.
Человек идет в магазин с целью купить нужный товар. И тут вроде бы просто понять, доволен клиент или нет – достаточно выяснить, нашел ли он то, что искал.
Но есть и дополнительные факторы, от которых зависит поведение покупателей:
-
как долго человек ищет товар и потом стоит в очереди на кассе;
-
чувствует ли себя при этом комфортно (психологически и физически);
-
соответствуют ли цены ожиданиям; и многое другое.
Что касается сферы В2В, то здесь большинству производителей не удается добиться гармоничного взаимодействия между элементами системы. В особенности если речь идет о нефти, алюминии, зерне, то есть о биржевых товарах. Тут чаще всего соприкосновения с конечным потребителем вообще нет. То, что реализуется в данной ситуации — это нечто вроде «ректификата», из которого «испарились» сопутствующие услуги.
Решение: провести анализ и систематизацию потоков формирования ценностей для покупателей в торговых объектах. При этом улучшение товара – это задача производителя. Ритейлер же отвечает за создание ценности изделия лишь в случаях, когда речь идет о результате работы его же торговой марки, фирмы.
Получение обратной связи от клиентов
В сфере В2В производитель и конечный потребитель никогда не пересекаются. В ритейле же покупатель сам приходит в торговый зал и чаще всего не против общения.
При этом влияние клиента может заметно отражаться на бизнесе, а может быть и совсем слабым. Тут имеет значение, по какой модели ведет дела собственник. Если для него увеличение потребительской ценности в приоритете, то, разумеется, он сделает организацию обратной связи частью всего бизнес-процесса.
К примеру, практически в любом супермаркете часто информация на ценниках не соответствует действительности. При этом иногда клиент отказывается покупать и практически всегда остается недоволен. Какой тут выход? Делать электронные ценники и четко определять для каждого товара свое место на полке. Во многих российских магазинах это уже практикуют. Можно еще дарить мелкие презенты посетителям, которые сами обнаружили неправильные ценники.
Источник: shutterstock.com
Так постепенно между поставщиком услуги и покупателем выстраивается продуктивное, долгосрочное взаимодействие. Клиент за свою лояльность (а не только за деньги) получает удовлетворение потребностей. Именно на этом, даже в условиях сильной конкуренции, держатся небольшие магазины, кафе, салоны красоты.
Решение. Когда во главу угла ставится создание ценности, то с клиентом необходимо налаживать партнерские отношения. Нужно постоянно «держать руку на пульсе» потребителя, следить, насколько он доволен, и подталкивать к обратной связи.
Главная составляющая в создании ценности – сотрудники
Это работает во всех случаях, когда бизнес делает ставку на непосредственное взаимодействие с клиентом. К примеру, в сфере предоставления медицинских, гостиничных услуг, в спортивных социально-культурных организациях и т. п.
Особенно заметна ценность сотрудников там, где самообслуживание сведено к минимуму, и продавцы должны активно консультировать посетителей (часто – когда речь идет о продаже компьютеров, лекарств и т. п.) Главным двигателем торговли становится именно продавец. А основной проблемой, кстати, могут быть жесткие скрипты, которых он вынужден придерживаться.
Решение. Нельзя ограничивать действия продавца строгим сценарием, это может не лучшим образом сказываться на эффективности взаимодействия с клиентом. Задача руководителя в бережливом ритейл-бизнесе – не просто контролировать, а всячески поддерживать коллектив, четко обозначать цели и создавать благоприятную эмоциональную атмосферу. Важно донести до каждого сотрудника, что и зачем делается в бизнесе.
Значение логистики и стандартизации
Логистические задачи в ритейле достаточно просты: переместить продукцию со склада в торговый зал, разложить её на полках и т. д. Но и эти процессы требуют управления и контроля, иначе корзины и стеллажи с товаром вечно будут хаотично разбросаны по магазину. В такой ситуации становится непонятно, сколько конкретно необходимо для данной работы персонала, техники. Как итог – лишние, необоснованные расходы.
Ночью продукцию принимают лишь некоторые магазины, а днем из-за пробок график доставок часто срывается. Для правильной организации движения товаров требуется стандартизация торгово-технологических процессов.
Иначе неизбежны потери при транспортировке, ожидании, простоях и т. п. Что становится причиной недостаточной стандартизации? – Плохо организованный менеджмент рабочих процессов. Как результат:
-
товар вовремя не разложен по полкам;
-
сотрудники перегружены работой (а это – потери).
Решение. К организации управления товародвижением необходимо подходить комплексно, с использованием специальных информационно-программных продуктов. Таких, например, как Stock-M (здесь применяется теория ограничений систем, то есть логика ТОС). С их помощью удается оптимизировать транспортные и иные материальные потоки.
«Встречный» материальный поток
Процесс создания ценностей принято представлять в виде двух потоков, материального и информационного. В сфере ритейла выделяют еще и второй (встречный) материальный поток, рассматриваемый как дополнительный. К нему относят: непродовольственные товары, которые не удалось продать в ходе сезонных уценок; просроченные продовольственные товары; оборотную тару; поток вторсырья.
На обработку этого встречного потока требуется довольно много времени, а появляется он по следующим причинам:
-
Короткие сроки годности (к примеру, это касается кисломолочных продуктов).
-
Трудности с прогнозированием покупательского спроса в конкретных торговых объектах.
-
Неверно выстроенная в торговой сети политика закупок и безответственное отношение к данному вопросу.
Две первые причины вполне объективны. Небольшие сроки годности у товаров остаются, если магазин находится далеко от поставщика, или в цепочке доставки есть еще несколько промежуточных звеньев. Либо эти сроки сами по себе невелики (для определенных продуктов вроде охлажденной рыбы и т. п.). Второй момент – спрос. Идеально его предсказать не способна ни одна из существующих моделей прогнозов.
А вот что касается третьего фактора – то это дело рук самой торговой сети. К примеру, если отсутствует процедура оценки потерь во встречном материальном потоке. Почему так выходит? Возможно из-за того, что продавец не несет материальной ответственности, когда возвращает поставщику товар.
Источник: unsplash.com
Либо (в непродовольственной сфере) владелец торговой марки осознанно выводит неликвид с рынка (и утилизирует его), чтобы сохранить спрос и уровень цен. Для монобрендовых объектов по продаже одежды и обуви это особенно типично.
Вообще встречный поток мешает процессу формирования ценности для потребителя и служит демотиватором для сотрудников.
Решение. С поставщиками нужно договариваться и сводить встречный поток к минимуму. Сеть 7 Eleven, например, это практикует. В день истечения срока годности товары уцениваются вдвое и отлично продаются. Есть компании, которые утром того дня, когда заканчивается срок годности, направляют продуктовые товары в социальные службы, занимающиеся организацией питания для малоимущих. Это придает встречному потоку особый смысл и ценность. Например, X5 Retail Group уже заявила, что возврат поставщикам хлебобулочных изделий осуществлять не будет, и к молочным товарам планирует применять эту же практику.
За счет принципов бережливого производства в ритейле вполне можно добиться повышения значимых показателей, следует лишь принимать в расчет определенные особенности данной сферы. А для полноты успеха нужно еще поработать над устранением факторов, из-за которых снижается именно операционная эффективность.

Где брать информацию по бережливому производству: список лучших книг про бережливое производство
Да, о бережливом производстве написана далеко не одна книга. Авторы рассказывают в своих трудах об истории формирования философии lean production, описывают её основные принципы, ценности, инструменты. Среди прочих, можно рекомендовать для прочтения следующие:
-
«Трудовые установки» (А. К. Гастев).
-
«Как надо работать» (А. К. Гастев).
-
«Моя жизнь, мои достижения» (Г. Форд).
-
«Открывая организации будущего» (Ф. Лалу).
-
«ДАО Toyota: 145 принципов менеджмента ведущей компании» (Дж. Лайкер).
По этим книгам вы ознакомитесь с основами бережливого производства и сможете составить себе представление о данной концепции.
Не лишним будет подчеркнуть, что бережливое производство – не панацея от всех бед при организации управления рабочими процессами. Для каждого бизнеса или компании необходимо выбирать свою управленческую стратегию, и всюду будут свои нюансы, детали и тонкости. А если не знаете, на какой методологии остановить свой выбор, то ознакомьтесь с основами каждого из рассматриваемых вариантов.